Home / News / Industry News / Aluminum die casts are often used as cathode in prefabricated buildings
Aluminum die casts are often used as cathode in prefabricated buildings
Jan.28,2023
Whether you are manufacturing a car or an aerospace component, die casting aluminum alloy parts are one of the most common processes. Die casts are lightweight and durable, which is ideal for manufacturing precise parts. They are corrosion resistant in both aqueous and atmospheric conditions. In addition, they have good electrical and shielding properties, which makes them a good choice for electronic housings and connectors.
Aluminum die casts are often used as cathode in prefabricated buildings, including curtain walling, windows, and shop partitions. They also have many aesthetic advantages. They are available in a variety of textures, making it possible to produce a wide range of surface finishes.
Aluminum die casting can be used in conjunction with machining and other materials. For example, electroplating is used to improve the functionality of aluminum die casts. Alternatively, you can also use chrome plating to improve the aesthetics of aluminum die casts.
Aluminum die casting can be used for a variety of parts, from power accessories to automobile engine fittings. Usually, aluminum alloy die castings account for 80% of automotive aluminum parts. They can be used in many applications, including automotive engine cylinders, pump shells, and motor end covers. These die castings are a great choice for manufacturing precise parts that can withstand high-temperature environments.
Aluminum alloy die castings can be made into automotive parts such as engine cylinders, engine valve bearings, and pump shells. They also have a variety of applications in other industries, such as prefabricated buildings and aerospace operations. These parts are lightweight and durable, and can withstand the highest operating temperatures. Aluminum alloy die castings are often used as parts for electronic connectors, which require a high level of durability.
Aluminum alloy die castings can be thermal treated for better shaping and corrosion resistance. This treatment increases the strength of the part and reduces internal stresses. It also increases the dimensional stability of the parts. The process includes controlling the heating temperature and the cooling rate. It also improves the machining performance of the parts.
Aluminum alloy die castings are used in an automotive industry that is in the process of developing new energy cars. The structural components of these new energy cars are more often produced by die casting. Automotive manufacturers are improving their safety, power, and lightweight in order to reduce their energy usage. In addition, automobile manufacturers are also developing in the direction of high quality and reliability.
Aluminum alloy die castings have excellent dimensional accuracy. The process can also embed inserts, complex fasteners, and other features. The process can produce parts that are durable, dimensionally stable, and can be manufactured without additional tooling. This makes it a versatile and economical process for producing parts. It also has high material utilization rates.
The most important features of aluminum alloy die castings include their good corrosion resistance and dimensional stability. However, they are not as strong as other metals, which makes them brittle under low temperatures. For this reason, you should choose aluminum alloy die castings that have uniform thickness. This uniform thickness will also reduce the chance of shrinkage porosity in the castings. You should also consider the draft angle of the castings. The angle should be reasonable to avoid scratches or surface defects on the cast surface. This angle also extends the life of the mold.
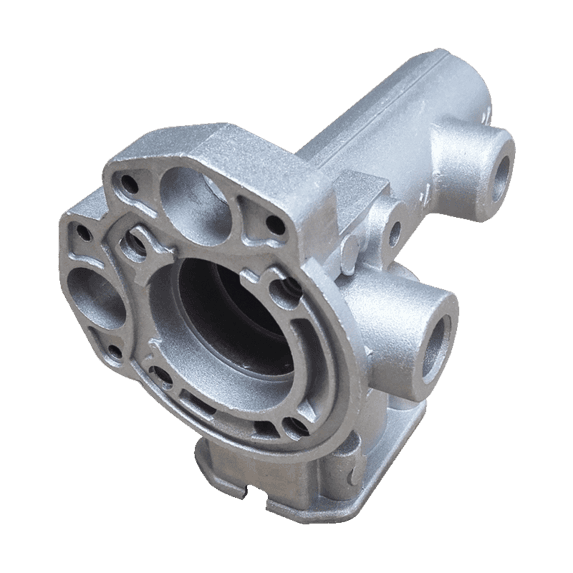