Home / News / Industry News / Tips for Post-Production Machining of an Alloy Gravity Casting Part
Tips for Post-Production Machining of an Alloy Gravity Casting Part
Feb.17,2022
Many parts require post-production machining. While some areas of the die will be visible, it is important to avoid these locations if cosmetics are an issue. These areas will need additional processing to remove material and meet tolerance requirements. Ideally, these critical areas should be located on one side of the die. However, some parts may require post-production machining. Here are a few tips for successful post-production machining. In general, ribs should be placed at the corners and edges of the part.
To prevent shrinkage after solidification, overflow wells can be used. Oversize patterns can be made by applying a rule that allows for a 5% oversize factor. When constructing a pattern that will match an existing part, it is important to measure and build the part with the same size and shape. This will ensure that it will shrink to the proper size. During the cooling process, the part should be cooled completely.
Oversize patterns are an important consideration in casting. Oversized patterns allow for additional molten metal during the solidification process. These oversized patterns are often made with a shrink rule, which entails making the die cavity a bit larger than the actual casting. The rule is mainly measured in percentages, so that the part will not be too small or too big. If a pattern is made to match an existing part, it will be constructed using a contraction rule.
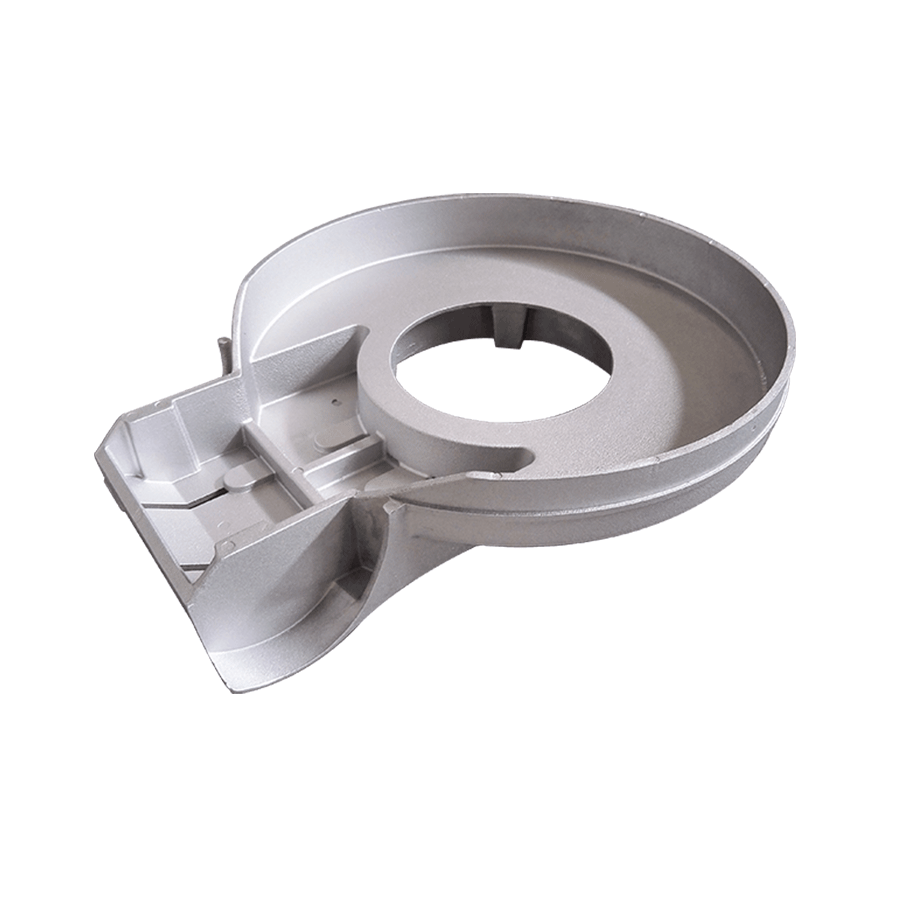
Overflow wells are important to prevent a casting from shrinking too much. If the overflow well is filled with molten metal, the result will be a part that is too thin or too thick. These overflow wells provide additional molten metal during the solidification process. As the casting cools, the overflow is attached to the part and must be removed. The material flowing through the channels does not fill the channels, so these should not be too large.
Oversized patterns are another consideration. Oversized patterns will minimize distortion caused by the solidification process. In addition, these oversized patterns are also shaped to mimic existing parts. In general, oversized patterns are not the same as standardized molds, but are made to fit the existing part. This will increase the chances of a successful cast with minimal material change. So, be sure to consult a professional for more information. They will be able to help you get the right casting for your needs.
Oversized patterns are also important in preventing cold shuts. The overflow wells help the product shrink. By making the part smaller, overflow wells can be prevented. Alternatively, overflow wells are designed to keep molten metal within the mold. When overflowing the mold, a small hole is created in the middle, which makes it less likely to crack. The smaller the hole is, the more the molten metal will flow into the cavity.